Priyam and Jane, as private consultants, worked on a large project, with PATH and Population Services International (PSI), to develop better toilets. This gave the team members valuable exposure to sanitation and new approaches to building toilets.
The project aimed to develop new toilet structures that would be faster to assemble, lower cost, and better quality than what was available.
We wanted to use local materials and skills, so that local businesses could take up manufacturing and selling these toilets in their areas.
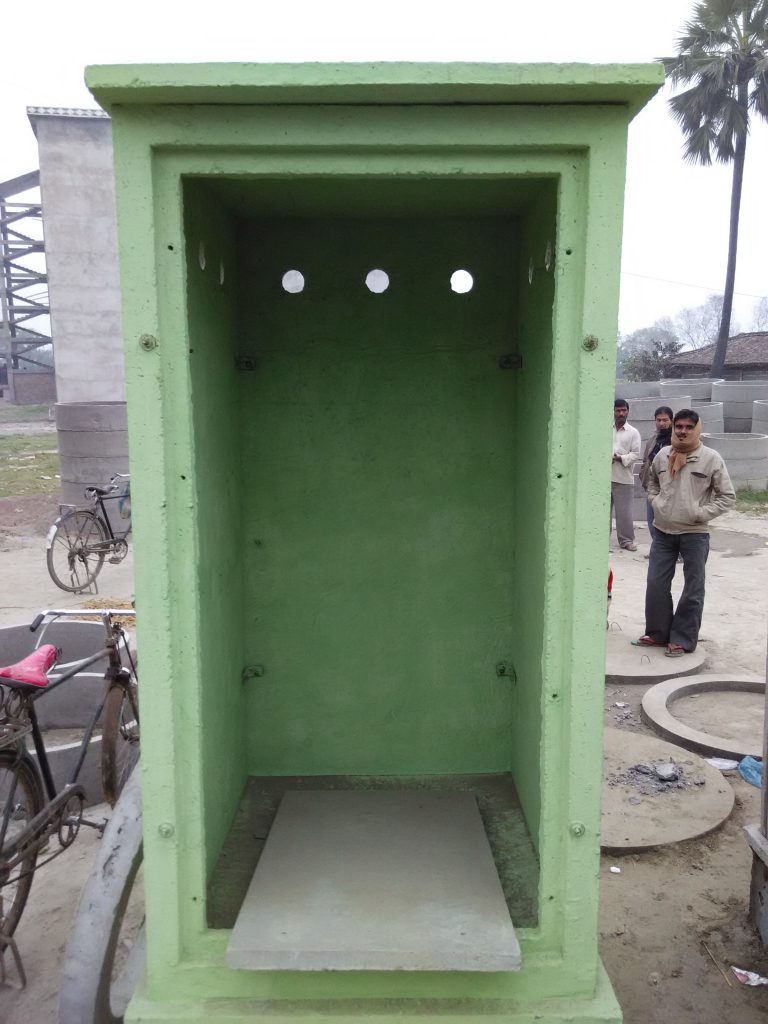
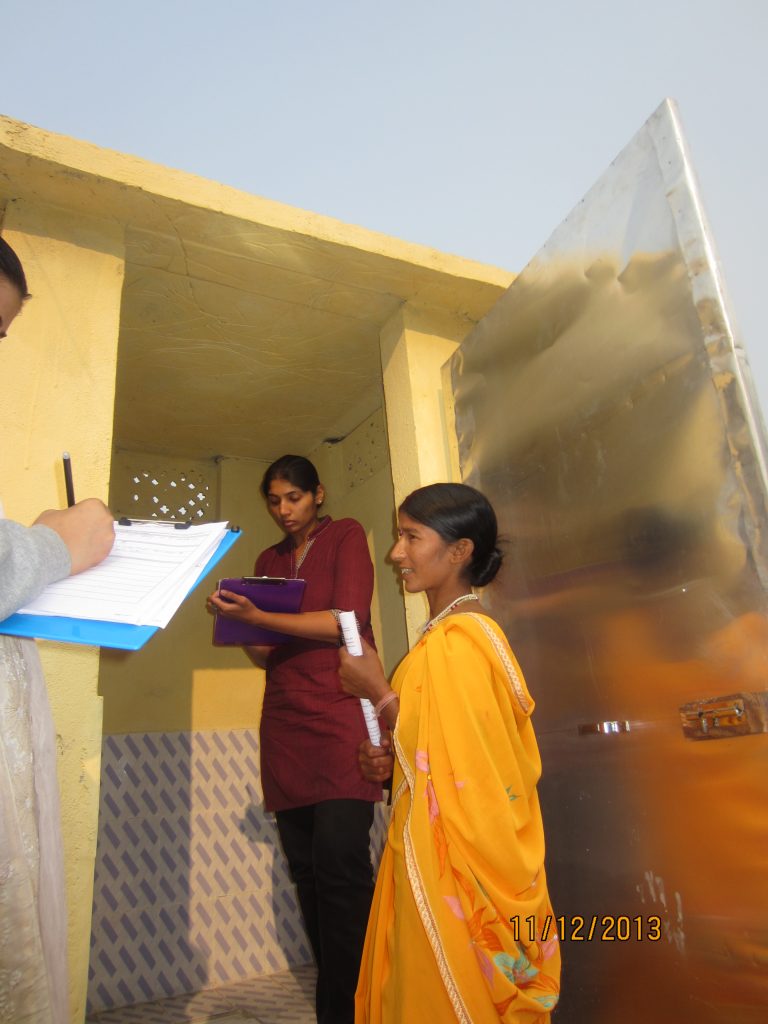
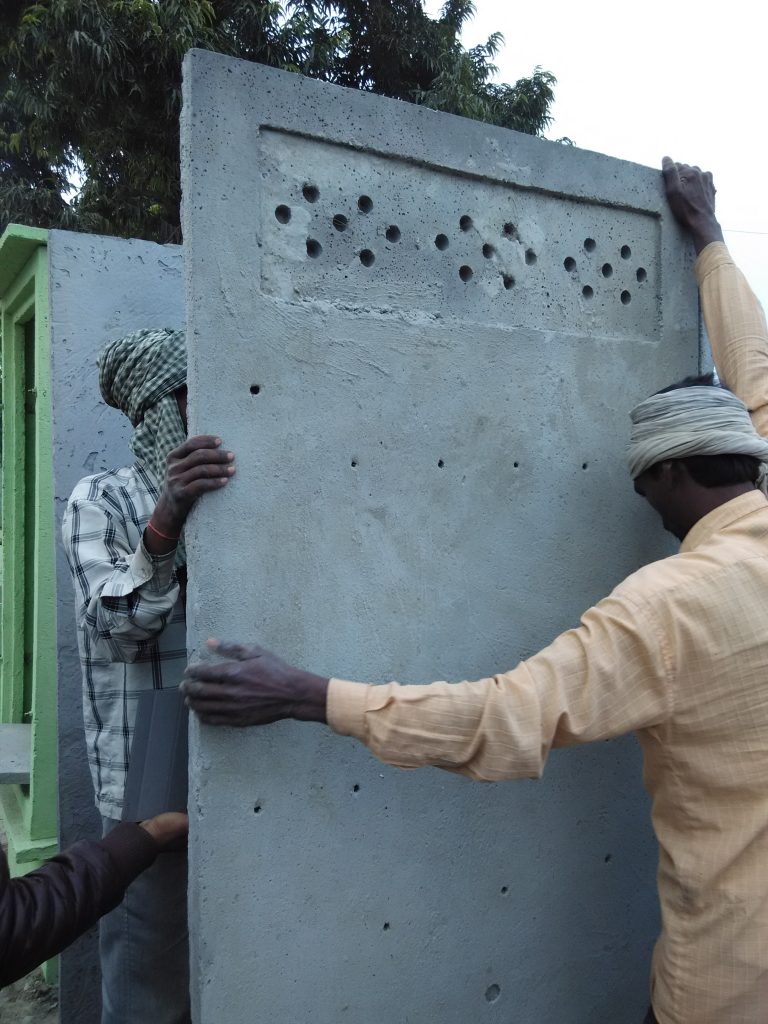
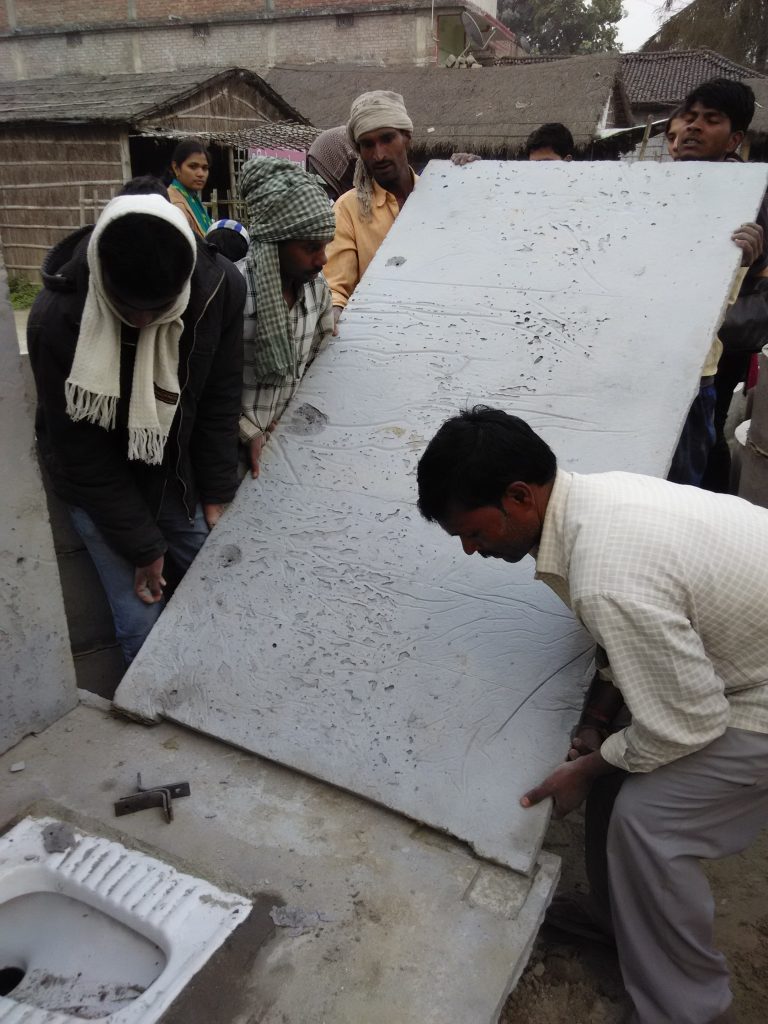
One of the most time-consuming steps that we observed when masons built conventional toilets, was the placement of the squat pan and the pipes and P-trap underneath the pan. The time taken to prop up the pan with bricks and level it and center it and adjust it, etc., was surprisingly long!
To speed up the assembly of the toilet, and to make the support of the squat pan stronger and longer lasting, we redesigned the installation of the squat pan:
We added precast beams and supports to the base of the Rapido toilet, so that the squat pan was simply placed on the beams, in the correct location, height, orientation, etc. Consistently.
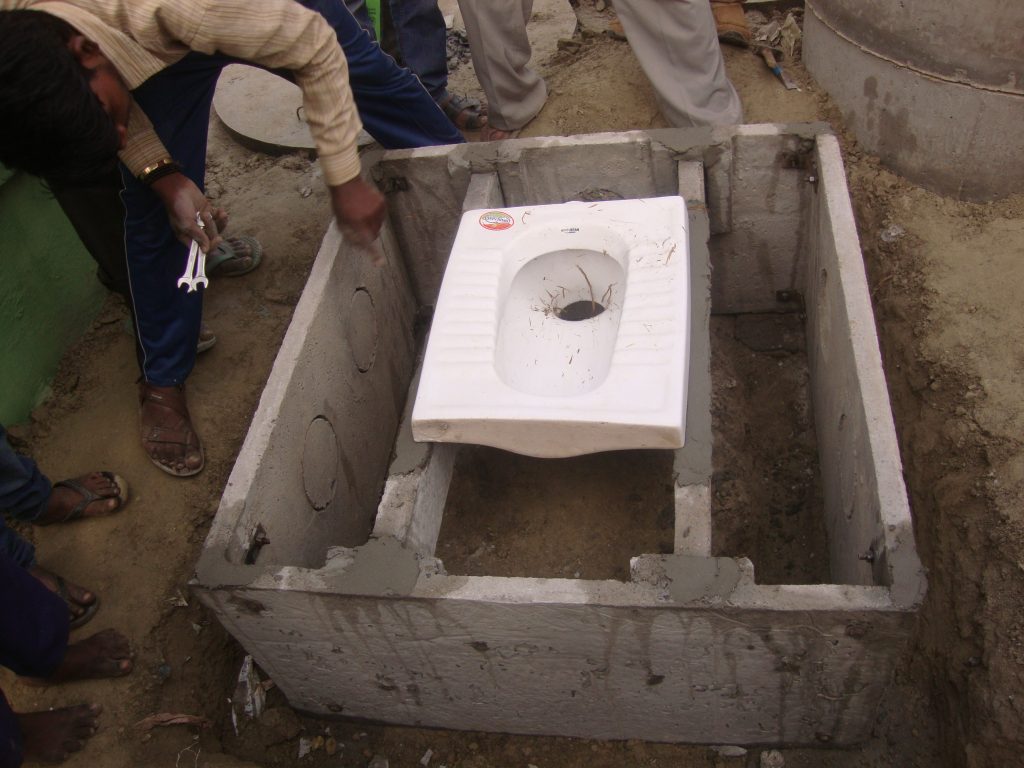